От механических цехов к умным системам: как начинается путь автоматизации
В российской промышленности ещё недавно слово «автоматизация» звучало почти как фантастика. Кажется, стоит вспомнить цеха, в которых до сих пор разливают масло вручную или выставляют упаковку на конвейере криком бригадира. Такие производства часто думают, что автоматизация — это для «очень больших» или «никогда не про нас». Но всё стремительно меняется: небольшие успешные кейсы появляются и в текстильной отрасли, и на пищевых предприятиях.
Самый яркий пример — завод, который ещё семь лет назад гремел порожними ящиками и хвастался опытом слесаря с 40-летним стажем, а сегодня управляет сортировкой материалов с планшета. В 2019 году на этом предприятии начали поэтапную модернизацию: первые шаги были просты — внедрили конвейер с датчиками веса. Это сразу срезало лишние трудозатраты и уменьшило пересорт. Через полгода уже анализировали на компьютере, почему и где случаются сбои. К концу года диспетчер видел подробную картину: сколько прошло сырья, кто работал у станка, где остановка. Это самое начало дигитализации, но для руководства это был шок — теперь каждый инцидент можно отследить, а информация прозрачна.
Другой производственный пример — отечественный химкомбинат, ещё в 2016 абсолютно не готовый к цифровой трансформации. Раньше водители развозили реагенты по бумажным накладным, а инженеры часами ждали команду на пуск насосов после ручных согласований. Всё изменилось после запуска системы SCADA: процессы контролируются через мобильное приложение, и настройка рецептур идет автоматически. Производительность выросла почти на треть, а потери на человеческом факторе почти исчезли.
Самое удивительное — не всегда механизация и первый уровень автоматизации требуют космических вложений. Например, пищевой холдинг в Екатеринбурге купил для экспресс-линии обычные фотоэлементы и поставил контроллеры «с рынка» вместо сложных иностранных решений. Через месяц устали работать вручную — вызвала автоматизацию. К концу первого года возврат инвестиций уже покрывал новые эксперименты.
Здесь важно трезво оценить стартовые возможности. Нет смысла сразу смотреть в сторону цифровых двойников или моделей на базе искусственного интеллекта, если ещё документы двигаются по коридору из рук в руки. Но если даже одни только датчики за месяц спасли цех от аврала, появляется вера в масштабный проект. В таких компаниях интернет вещей сначала помогает людям — сокращает монотонную работу, делает ошибки явными, а данные из конвейера — общедоступными.
Три уровня промышленной автоматизации: реальные отличия на практике
В разговорах об индустрии 4.0 часто крутятся термины про «уровни автоматизации», но за ними бывают вполне конкретные изменения процессов. Пример — предприятие из Татарстана: раньше вопросы «где поставить кран?» решал начальник смены, полагаясь только на опыт. После внедрения MES-системы (Manufacturing Execution System) ситуация перевернулась. Каждый шаг виден как на ладони: какая партия у кого на руках, какие операции уже завершены, а где зависли из-за брака. Это не только контроль, но и сочная аналитика для роста.
Эксперты любят выделять три ключевых этапа автоматизации:
- Механизация и диспетчеризация — когда внедряются базовые контроллеры, датчики, конвейеры. На этом уровне автоматизация проста: заменили ручные операции на автоматические, добавили телеметрию. Пример: хлебокомбинат, где время выпечки и температура теперь всегда под контролем, а остановки фиксируются автоматически.
- Интеграция управления и обмена данными — тут появляются системы класса SCADA, MES, интеграция со складом и логистикой. Полотно данных становится цельным, люди тратят меньше времени на ручной учет. Это хорошо видно на машиностроительном заводе: появилась синхронизация работы станков, а заказы прослеживаются от поступления до отправки заказчику.
- Цифровые двойники и искусственный интеллект — самая верхняя планка, где уже нет сомнений: почти любое решение можно смоделировать заранее. Например, ведущий металлургический концерн России сначала создал виртуальную модель своего прокатного стана: теперь новые рецептуры могут «прокатать» в цифровом пространстве. Если что-то идет не так — корректируют настройки до запуска реального оборудования.
Частый вопрос — как понять, на каком уровне ты находишься? Понять просто: если большинству операций всё равно нужна подпись на бумаге, а оцифровка только в планах, вы на первом уровне. Если вся информация о производстве под рукой, а все заказы и партия автоматически проходят прозрачный учет — это уже серьезный второй уровень. Попробовать «проиграть аварию», спрогнозировать нагрузку, протестировать новые процессы на виртуальной модели — вот это уже цифровая зрелость.
Подробно узнать про промышленная автоматизация уровни можно на профильных сайтах, где примеры разложены по полочкам: от вводных историй до практических нюансов развертывания электроники и ПО.
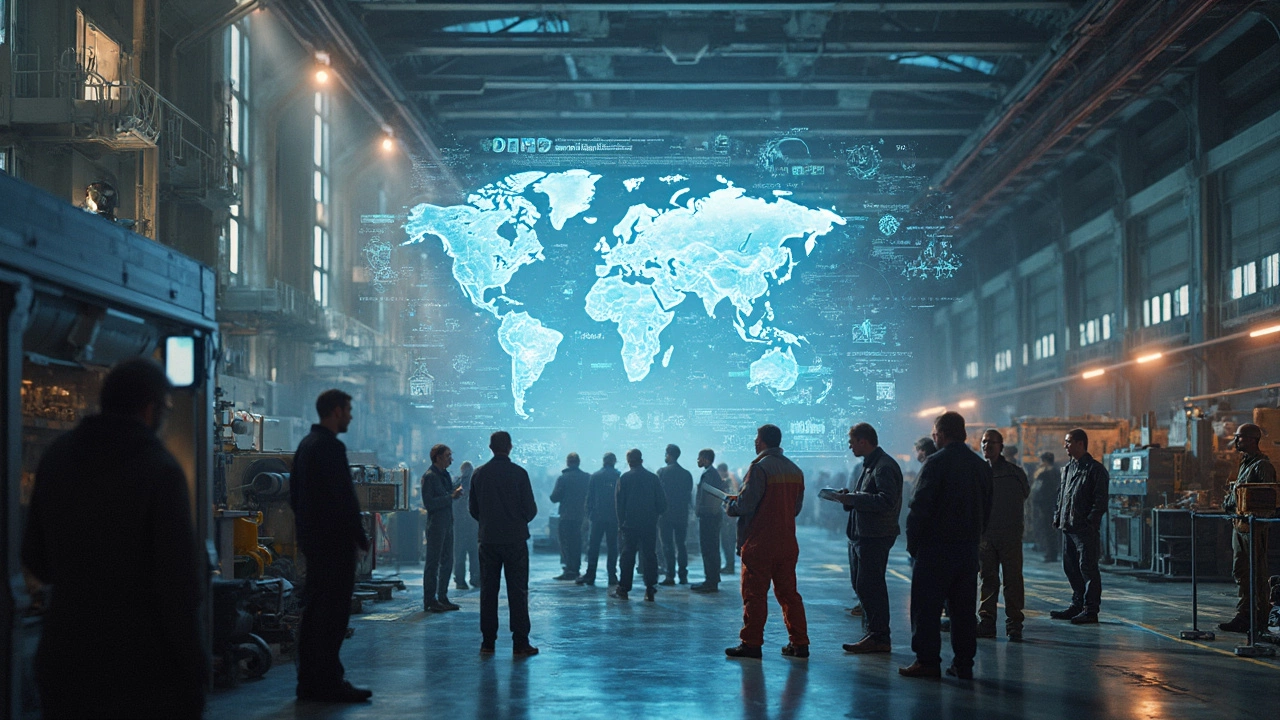
Практические кейсы: кто и как прошёл путь от механизации к цифровым двойникам
Сложно поверить, но даже такие гиганты, как «Северсталь» или «СИБУР», ещё 15 лет назад больше напоминали классические советские предприятия с огромными штабами и ручным распределением смен. Переход к автоматизации был не только технической задачей — ломать приходилось привычки тысяч сотрудников.
«СИБУР» начал с цеха энергообеспечения. Задача казалась невыполнимой: синхронизировать работу десятков насосных агрегатов в режиме реального времени, сократить выбросы и дать диспетчерской актуальную информацию. Для этого собрали команду ИТ-инженеров и рабочих. Прямо на месте смонтировали датчики потока, температуры и давления, которые сразу вывели в SCADA. Через полгода аналитика показала 12% экономии топлива — за счет банального отказа от дублирующих запусков.
На другом предприятии — Красноярском алюминиевом заводе — поэтапно внедрили три уровня автоматизации. Сначала просто автоматизировали транспортную систему сырья, потом подключили всю логистику к центральной SCADA. Итог? Среднее время простоя в месяц снизилось с 45 минут до 5. После перехода на цифрового двойника любого участка руководители могут «прокрутить» гипотетическую аварию — это сократило аварийные простои почти до нуля.
Компания | Уровень автоматизации до цифрового двойника | Результаты |
---|---|---|
СИБУР | SCADA + большая интеграция IoT | Экономия топлива 12%, сокращение аварий и ручного труда |
Красноярский алюминиевый завод | SCADA постепенно переросла в цифровой двойник | Снижение времени простоя почти до нуля |
Небольшой пищевой холдинг | Фотоэлементы и базовая телеметрия | Старт автоматизации с возвратом инвестиций уже в первый год |
Есть ещё один интересный пример: средний машиностроительный завод в Ульяновской области, который до сих пор производит детали для военной и авиационной техники. Руководство не верило, что «их специфика» подходит для цифровизации. Начали с малого — подключили датчики работы станков, ввели автоматическое оповещение об остановке. Дальше интегрировали заказчика в цепочку: теперь клиент видит этапы работ в реальном времени через защищённый веб-сервис. Следующим шагом станет тест цифрового двойника для оптимизации расписания ремонтов.
Здесь есть важный лайфхак: на каждом этапе стоит «обкатывать» изменения на одном участке. Если модель работает — масштабировать решение. Такой подход сокращает риски и позволяет быстро адаптировать рабочие места под новые технологии.
Цифровой двойник: как он изменил стратегии крупных и средних заводов
Наверняка встречались новостные заголовки о том, что теперь каждое новое оборудование будет сразу строиться вместе с цифровым двойником. Это не выдумка маркетологов. Уже в 2024 году министерство промышленности сообщало: у 18 из 25 ведущих российских промышленных предприятий цифровые двойники развернуты минимум на одном участке.
Бизнес быстро понял главную выгоду — симуляция позволяет тестировать идеи без риска потерять деньги или подвергнуть людей опасности. Например, крупный химический завод в Тольятти использует двойника не только для прогнозирования брака, но и для «обучения» новичков: сотрудники проходят практику виртуально в реальных условиях и учатся управлять опасными процессами.
В машиностроении цифровой двойник позволяет заранее выявлять слабые точки оборудования. Инженер открывает 3D-макет, загружает реальные параметры, смотрит, где появится перегрев, какой подшипник выйдет из строя раньше. Ремонтная служба теперь не реагирует на аварию — она предупреждает её.
Средний фармацевтический завод внедрил двойника для проверки новых рецептур и технологических схем. Результат — экономия сырья до 8%, переходы между партиями сократились по времени почти вдвое. А отдел качества вместо «ручного отбора проб» теперь получает виртуальный отчет по каждой партии.
Секрет здесь в том, что цифровой двойник не появляется из ниоткуда. Он строится поэтапно: сначала фиксируются все производственные параметры (температура, давление, скорость, состав сырья), потом внедряется аналитика, а на следующем шаге — симуляция процессов. На этом этапе важно хорошее взаимодействие между рабочими, ИТ-шниками и руководством.
Распространённый совет — не торопиться запускать двойника на всём производстве. Лучше выбрать самый критичный участок, где есть массовые сбои или большие потери. Когда результат станет явным (снижение аварий, экономия энергии, улучшение выпуска), остальные цеха сами начнут спрашивать: «Когда нам?».
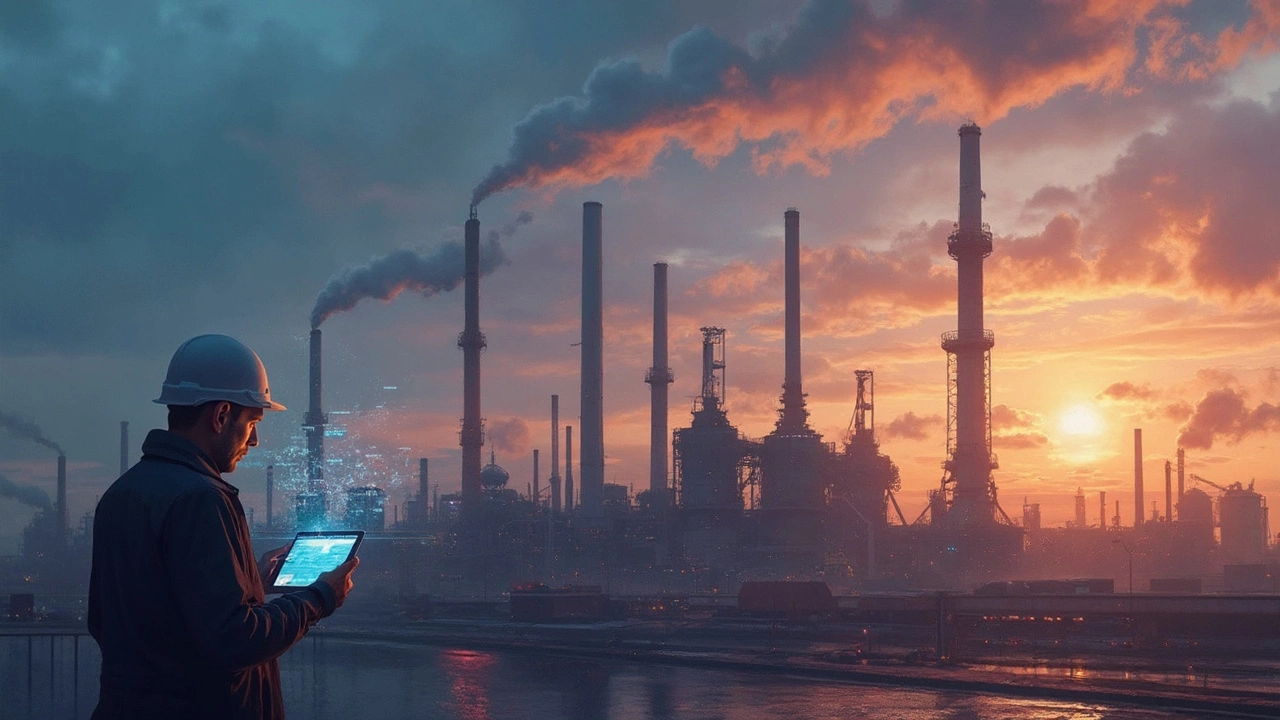
Что мешает быстро перейти к цифровым двойникам — и как заводы обходят эти барьеры
Главный страх всех директоров — что автоматизация и цифровизация сорвут работу, потребуют уйму денег и вызовут отторжение у коллектива. Но опыт показывает, что большие перевороты почти всегда происходят постепенно.
Стартовать, как правило, мешают три барьера. Первый — человеческий фактор: сотрудники боятся, что их заменит робот. Второй — сложность интеграции со старым оборудованием. Третий — нехватка объективных данных: руководство просто не видит, где прячутся издержки.
Компании обходят эти барьеры хитро. Лучший прием — сделать цифровизацию «своей», а не спущенной сверху. Когда рабочий сам предлагает провести аналитику просто для экономии сил, а ИТ-шник вместе с ним выезжает «на линию» и показывает, как работает датчик — сопротивление падает. Один завод в Краснодаре даже провёл конкурс среди операторов на лучший способ цифровизации мини-склада, и самые активные сами стали волонтёрами-проводниками цифровых изменений.
Интеграция со старым оборудованием — не приговор. Часто достаточно добавить интерфейсный адаптер, чтобы собрать ключевые параметры. На целлюлозном заводе так «оживили» даже советские линии 1980-х годов — просто подключили Wi-Fi-модуль к старому контроллеру. Данные старое железо отдаёт новым аналитикам, которые, наконец, понимают, как действительно идёт производство.
С данными ещё интереснее. В одной пищевой компании до цифровизации руководитель не мог сказать, сколько продукции выходит в смену. После внедрения простейшего контроля через камеру и электронные весы, выяснилось: загрузка линии 70%, а потери — в цеху упаковки. Вывод напрашивался сам собой — автоматизировали узкое «горлышко».
Вот небольшой список советов, которые работают на реальных производствах при запуске автоматизации:
- Ищите самый проблемный участок и автоматизируйте его первым — результат убедит даже самых скептичных.
- Не пытайтесь внедрять сразу все уровни автоматизации — любой этап должен давать ощутимый результат за 1-3 месяца.
- Обязательно подключайте рабочий коллектив: снимайте страхи, показывайте пользу для самих сотрудников.
- Делайте автоматизацию прозрачной: пусть результаты будут на виду у всех.
- Используйте опыт других предприятий — сейчас отраслевое сообщество делится инструкциями и ошибками открыто.
Итог тут простой: путь к цифровому двойнику начинается с маленького датчика и большого желания. Важно не идеализировать технологии, а делать выбор сознательно — и тогда даже на самом старом заводе появится шанс обойти конкурентов, которые ещё спорят, – нужен ли контроллер на линии.
Написать комментарий